Manufacturing Process Analyst
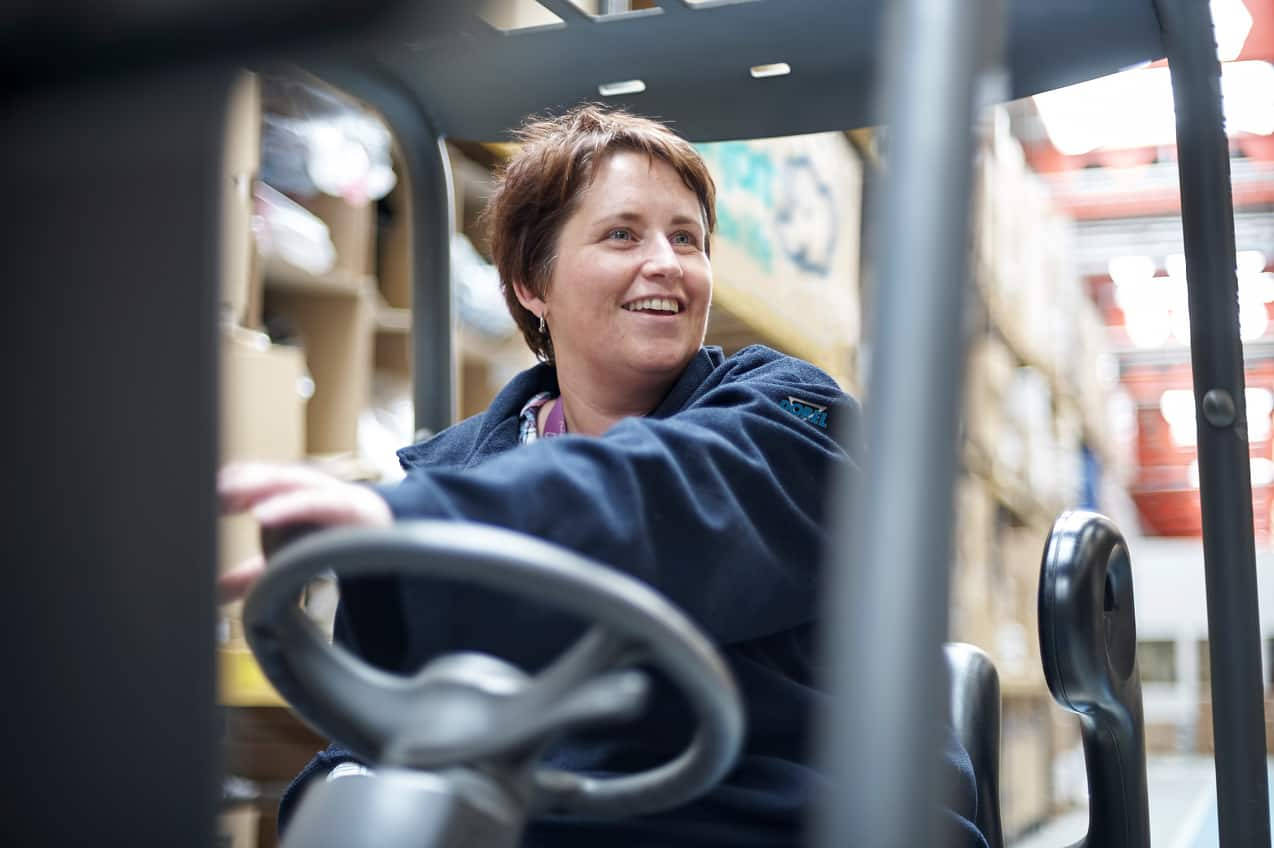
About us
• Dorel Industries Inc. (TSX: DII.B, DII.A) is a global organization, operating two distinct businesses in juvenile products and home products. Dorel’s strength lies in the diversity, innovation, and quality of its products as well as the superiority of its brands. Dorel Juvenile’s powerfully branded products include global brands Maxi-Cosi and Tiny Love, complemented by regional brands such as Safety 1st, BebeConfort, Cosco, and Infanti. Dorel Home, with its comprehensive e-commerce platform, markets a wide assortment of domestically produced and imported furniture. Dorel has annual sales of US$1.7 billion and employs approximately 4,200 people in facilities located in twenty-two countries worldwide.
Your mission
Under the leadership of the Director of Technical Services, the Manufacturing Process Analyst will supervise and execute the work of the industrial engineering department. They will develop, implement, and facilitate activities that improve processes and systems supporting overall Product Setup, Product Manufacturing, and Engineering Changes. This individual will focus on optimizing ERP system configuration, developing engineering change strategies, and streamlining standard processes to improve productivity of the Industrial Engineering Department and Manufacturing Efficiency.
Key responsibilities
Key Responsibilities
- Serve as the thought leader for technical business processes that promote increased efficiency and productivity on multiple levels.
- Develop detailed BOM’s for all new Columbus made SKU’s and changes to existing SKU’s.
- Develop manufacturing cost estimates for new products and changes to existing products.
- Support new product development process by providing input to insure accurate, logical, and consistent BOM product structures & subassemblies.
- Identify opportunities to reduce waste and increase productivity in manufacturing and manufacturing support activities.
- Maintain labor management system based upon engineering standards that accurately report predicted and actual labor activity.
- Update and maintain capacity planning tools.
- Create and update manufacturing process flows and update manufacturing floor layouts.
- Develop product pallet stack patterns and recommend optimized warehouse & trailer space utilization.
- Participate in development of PFMEA’s and Control Plans for new products and major changes to existing products.
- Seek improvements in ergonomics and safety.
- Supervise industrial engineering technical personnel.
Your profile
Experience and Skills
- Minimum 3 years’ experience in a manufacturing organization.
- Skilled in enterprise resource planning (ERP) tools.
- Ability to accurately estimate product cost.
- Experience in labor analysis and costing.
- Track record of continuously improving workflows.
- Knowledge of work sampling.
- Ability to create and modify process maps.
- Proficient in Microsoft suite applications
- Good interpersonal skills
- Working knowledge of Visio and Cape Pack software
- Experience with other analytical techniques such as labor time studies, Lean, Kaizen, PFMEA, etc.
Education, Licenses, and/or Certification Requirements:
Bachelor’s Degree or equivalent
Are you ready to grow with us?
All of our talented employees share the same mission: to Care for Precious Life. We help families live carefree lives by providing them with juvenile products with the highest safety and comfort standards. Our frontrunner mentality matches our position as a global market leader. Being first means we forge our own path, we explore new ways to enhance our brands. We are continuously reinforcing our leading position and believe that team spirit, personal drive, and accountability can make a real difference in achieving sustainable growth.